DNATA
Load Control
On The Mark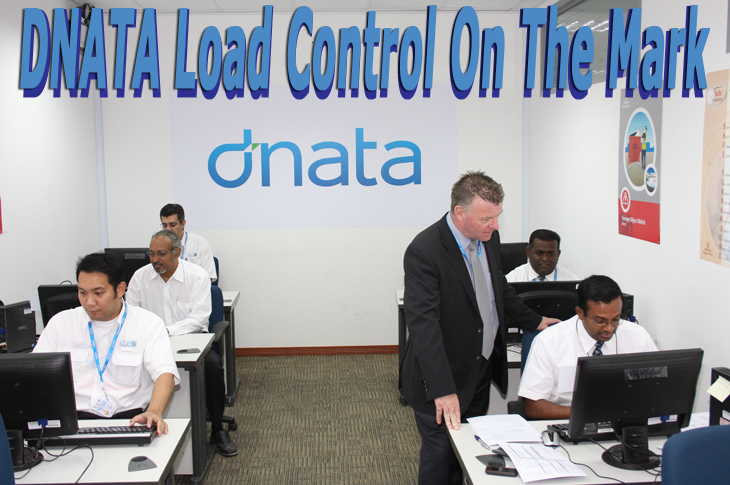
What
is dnata Load Control Center? How many people work for the company &
where?
The
dnata Load Control centre is part of the dnata airport operations control
centre , it is a state of the art centre located just outside the perimeter
of Dubai Airport, it has 120 work stations all with system access to
all DCS systems and internet; the staff can also access all operational
systems for both dnata and Emirates from these work stations. The number
of Load Control Staff is 250 producing in excess of 19,000 load sheets
per month for Emirates/Fly Dubai and 135 other airlines who operate
out of Dubai.
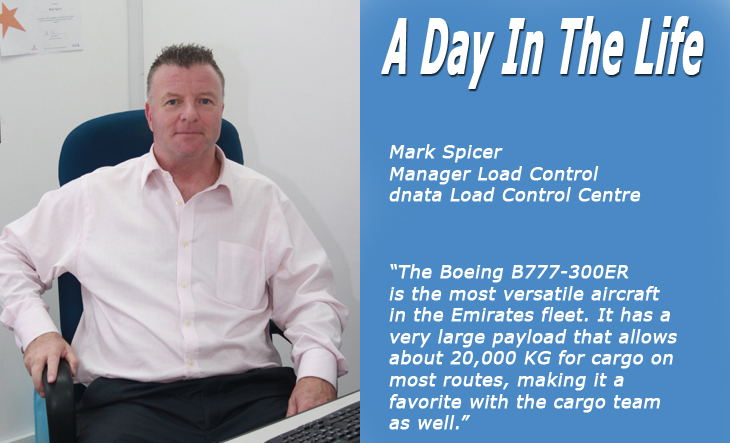
Describe
a typical day to Mark Spicer hour by hour.
I
start every morning at 05.15 and visit the gym at 05.45 for a 30-minute
aerobic workout, which sets me up for the day, reaching the office by
06.45.
I check my diary to see what’s
planned for the day and read all the reports from the previous 24 hours
and analyze any failures or issues that might improve the business.
I then conduct a team meeting with my direct reports and discuss the
underlined issues, task the team with arranging meetings with the staff
and discuss operational improvements.
When these meetings take place I
make sure and attend them. These are varied because Load Control is
a stake holder in almost every department in Dubai Airport. I also visit
the 2 load control satellite offices in Dubai Airport, (we have 2 offices
in the airport where a number of staff are located to handle manual
flights and any airline specific needs). My purpose is to review any
on-going projects with my project manager and get a status update. I
also set up a customer visit based on someone who requires a face-to-face.
Usually it is one customer during a week.
I find that I spend at least 2 hours
a day answering e-mails and general admin duties, P2P’s/ITSR’s/Updating
PM’s/budget data/daily performance data.
I leave the office for home between
04.30 & 05.30 and arrive home at around 06.00, grab dinner and then
go on the laptop to see if any new requests have come in, check to see
if I missed any mails, (I do like working at home as it is tranquil
and I don’t get interrupted). This for me is a normal work day.
On the weekends I still get up at around 05.30 but usually go cycling
or a road trip on my motorcycle into the mountains in Hatta.
Can
you briefly walk us through load control planning for a B777C aircraft?
We
are very fortunate to have a good team within Emirates SkyCargo who
oversee the build-up of the cargo after its acceptance. As all members
of the team are not only experts in cargo handling, they are also fully
trained load masters so they are able to enter the cargo into the correct
contours and units, envisaging its final loading.
When we receive the final unit
weight statement from cargo we simply locate the loads to ensure the
dangerous goods are segregated correctly and ensure we keep the lateral
balance as low as possible to ensure we aren’t penalized on the
take-off weight. However, when we have odd-sized shipments like the
drilling pipes that we recently carried for a client it is always slightly
different. In this case, we worked closely with the Cargo team to not
only create a load plan that could carry all the load but also reduced
the loading and offloading times. In this particular example, this was
achieved by maximizing the use of crushable pallets to avoid the need
for straps (120) to secure the pipes, without the crushable load we
did not have the need for the straps, which would take hours to fix.
Thanks to the expertise and the close communication between Load Control
and Cargo we managed to ensure the use of the straps was kept to a minimum
and thus reduced the ground time to ensure the aircraft was available
to operate its next sector on time.
Would you also briefly explain how the process might differ for the
same aircraft in passenger variant but also include the belly cargo
discipline?
Planning
of the passenger aircraft is more of a challenge than the freighter
variant due to the variable profiles of passengers, baggage and cargo
on any one flight - but this ensures that no two flights are the same
and thus reduces the monotony that can creep in when you follow the
same routine day in day out.
Our planning starts 10 hours before
the departure, we first calculate the baggage requirement based on the
booked passenger load, once this is complete, cargo also starts planning
to maximize the remaining space. When
we receive the final cargo figures two hours before departure, we then
try to ensure we can uplift the maximum possible revenue, but without
compromising on safety. Firstly, we will check the go show priority
of the cargo and select the appropriate hold version that will allow
us to maximize space. We then start to locate the cargo and baggage
to ensure that all the temperature-critical cargo is in the correct
hold, the dangerous goods are segregated accordingly and the baggage
is planned so that the priority and transfer baggage can be offloaded
quickly at the next station.
All of this is done whilst also
taking into consideration the connection times and travel distance of
the ramp transfer cargo and at the same time also trying to ensure an
optimum trim to reduce fuel costs.
Describe loading characteristics…what airplanes are a “dream”
to work with and which ones in your years have been or are most challenging?
The
Boeing B777-300ER is the most versatile aircraft in the Emirates fleet,
it operates almost limitless possibilities of possible loading combinations,
it is the ideal aircraft to be used on multi sector flights and you
can avoid any possible over-stowing of loads. It has a very large payload
that allows about 20,000 KG for cargo on most routes, making it a favorite
with the cargo team as well.
The new A380-800s however, are more
of a challenge. The passenger configurations are great for passenger
convenience, but it does mean that the aircraft is very nose-heavy and
with the majority of the hold space in the forward it makes it difficult
to trim. The aircraft also has unique peculiarities, not normally encountered
on a modern passenger aircraft, which require a lot of extra focus.
In truth however, there are no bad aircraft to work with, the biggest
problem faced is the unpredictability of load due to the profile of
the passengers who transit through Dubai. I am fortunate and grateful
that I work with a good team who can adapt to these challenges so easily.
You have been at this job for 24 years. Tell us which incidents of poor
load control stand out in your mind?
This
is a rather difficult one to answer -thankfully in my 24 years I’ve
never been part of an incident or accident directly attributed to load
control. That being said, in my previous company we never focused on
Ideal Trim, it was acceptable to be anywhere within the trim level,
and there was no information of fuel cost or extra cost of a poor trim.
I now see this as poor load control. My previous company never focused
on maximizing space as we do in my team, often flights would have cargo
off loaded when there was no need to, it all comes down to your planning.
How do dLCC activities square with environmental issues?
We
try and do as much as we can, where we can. We are the leaders in fuel
cost savings and focus on reducing fuel cost for aircraft, this is not
only for profit but has a large part to play in helping the environment.
In addition we have a paper saving
project and on-going energy saving projects in our office facility.
What sort of fuel impact do you have? What other initiatives are being
taken to enhance green focus at dLCC?
Last
year through our ITL project we were able to save Emirates an estimated
25 million dollars in fuel, just by getting better trims and the aircraft
flying more efficiently and we are looking into more projects and initiatives
to enhance the green-focus further in our line of operation.
dLCC serves we understand, 140 customers in Dubai and even more worldwide,
Why should an airline say in Australia consider utilizing dnata Load
Control Centre?
We
are the experts in Load Control, we have 250 trained staff who handle
12+ DCS systems, this is unusual as most handling agents only handle
a couple of airlines and are not familiar with so many systems and procedures.
Our expertise will deliver a cost saving
product to any airline that tasks us with reducing their fuel cost.
Our cost base is low so in turn, we can deliver load control at a competitive
price, thus reducing the cost of handling load control by the airline
(as the airline will not need to train their own people and will not
have a large cost attributed to load control).
What
did you study in University? How did you get into load control?
When
I left school I studied for a CIG London in Motor Vehicle studies, once
qualified I changed direction and became a service engineer in Catering
& Vending. I joined BA in the 80’s as a ground agent and worked
my way through the ranks in all areas of BA and several different stations,
I then went back and studied Management at Oxford Brooks University
in the 90’s as I needed to gain a formal management qualification.
Does/has
load control ever felt like a high wire walk?
We
are aware that we are handling the lives of 100,000 of people every
day but we are confident in our approach to safety, we have excellent
procedures and processes in place and most activities are backed up
with a safety process, either system or people-based. To answer your
question “ Yes” it’s a stressful position, maybe the
most stressful in the airline, but with a good team around you and good
training and recruitment of quality people, the job is a lot easier.
How do you balance your life? Hobbies/Sports/Music/Favourite City/ Family/Vacation
Spot?
I
use the gym as stress relief and try to balance my life, I love cars
and motorcycles and own a Subaru WRX Sti performance car and 2 motorcycles
- a ZX10 sport bike and a KTM 450 dirt bike, weekends are spent in the
desert on the dirt bike or at track days racing my sport bike around
the autodrome.
I play golf with a handicap of 9, my
favourite city is Perth and my favourite music is R&B. Vacations
are varied but LA/SFO and Vegas are where I’ve been for the past
4 years. I have two children, a 25-year old daughter and 23 year old
son, my daughter has just had a baby boy so I’m now a grandfather.
What would you like to see changed about the way Load Control is perceived
by others and conducted?
Load
Control (LC) is the silent hard working side of the business, there’s
no glamour in LC so it’s often overlooked. I would like to keep
driving awareness of how important it really is, if we continue to show
cost saving statistics I’m sure if will get more favourable press.
What can be done better?
With
the advances in computer systems and in technology we can improve trim’s
and save money for airlines. In a world of growing cost we need to improve
systems that can support the cost-efficient delivery of LC and ultimately
reduce fuel and result in cost savings.
What interaction do you have with others involved in what you do who
are not working for you or a customer? What trade shows? What reading
material?
There’s
very little written about LC and rarely do we see trade shows publicizing
it. Aside from the industry contacts and my team I would like to start
visiting a few more trade shows to increase my interaction.
What do you consider to be the biggest challenge today in load control?
Is it an industry issue? Education?
The
biggest challenge we face is the need for continual improvement - we
need to create modern systems that support the decision making of Load
Controllers, Optimum trim and maximizing payload - this is where profit
and efficiency can be increased.
Geoffrey
|