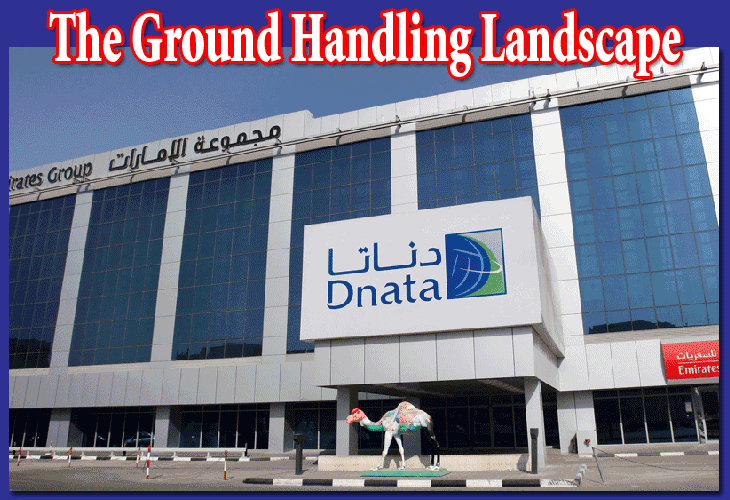
Trends and fads in the
industry come and go: at one time, airlines strived to become conglomerates,
adding the “Group” title to their names and accumulating holdings
from hotels to catering and aircraft maintenance to IT and logistics,
epitomized by the likes of Jan Carlzon at SAS, Philippe Bruggisser at
Swissair/SAir Group, and Robert Crandall at AMR Corporation and American,
to name a few.
The flight in the opposite direction followed
a couple of years later, with a nearly myopic focus on “core competencies”
that evolved in the 1990s, resulting in many airlines eventually shedding
services considered non-core. These developments were by no means linear
or uniform; however, they spawned a slew of new organizations, which,
while starting nationally or regionally, have since expanded to become
global in scope, as is the case with some of the ground handling companies.
HACTL (Hong Kong) started operations in
1976; Swissport was founded in 1996 and acquired Servisair in 2013; Fraport
was incorporated in its current form in 2001; Aviance emerged in 1999;
AMR eventually became WFS; DNATA went global and operates as Toll/DNATA
in Australia while ASIG grew incrementally and expanded worldwide, and
there are too many others to name individually.
These ground handling companies have been around for two decades or longer
and perhaps nowadays only graybeards still recall a time when airlines
used to self-handle cargo. Frankfurt Airport is not unique in actually
having handling companies dedicated to building up and breaking down cargo,
and another unrelated handling company servicing the airside, i.e. ramp
operations and loading/offloading aircraft.
It is perhaps timely to take a look at what
this has done to the airline cargo business when cyclically, yet again,
the focus is on chronically bemoaned excessive dwell time. There doesn’t
seem to be a single, one-size-fits-all, answer, opinion, or practice among
airlines when it comes to this subject. One the one hand, having a vendor/customer
relationship between airline and ground handler can bring benefits based
on a structured SLA (service level agreement) and also financial predictability.
On the other hand, ground handling companies service multiple airlines
and are expected to indiscriminately provide the same quality and attention
to each. That at least is the theory, but the results vary. The counterbalance
is as always in the detail—it isn’t unusual, for example,
to see ground handling staff dedicated exclusively to each customer airline’s
IT system because the airline insists its system needs to be used to process
its cargo. This is at a time when there are a number of highly successful
handling systems in place, which interact electronically with airline
cargo systems—yet the customer is king!
If one where to examine some of the typical
problem areas in the airline/handler relationship, primarily as it relates
to either added effort, or more importantly, what may impact dwell time,
what comes up is the interdependence and timeliness of data entry, message
exchanges for shipment status, and ULD control. Waiting times for customers’
trucks delivering and/or picking up freight are also entirely controlled
by the handling company.
Is the complexity and lack of direct control
therefore, to an extent, a self-created problem by the airlines? Is it
too late to change? One can examine what various carriers are doing in
this respect; Delta Air Lines, which carries cargo solely in the lower
decks and bellies of passenger aircraft, maintains a mixed environment,
with handling agents in most network locations except its largest operation,
the Atlanta hub, which has been self-handling its cargo and that of its
SkyTeam partners since soon after Neel Shah and Ray Curtis were brought
in from United to take over in 2008. Delta also has its office staff at
several airports processing cargo documentation in conjunction with a
handling company performing the physical cargo processing in the warehouse
and airside.
In
a 2006 FlyingTypers article titled “Dolan
Gets Upped-Talks About Change” Scott Dolan, President-United
Cargo said:
“In June 2003, United Cargo began
outsourcing of our largest domestic warehouses—including those at
our hubs. This was an initiative that not only saved about 80 million
dollars annually, but also enabled us to significantly improve service
to our customers by implementing more robust metrics and tough service-level
agreements with our vendors.”
Dolan went on to say: “I have to admit;
we had a rough start in the first year because we did not do the work
necessary to be successful. You need to have documented processes, metrics,
SLAs and a reward & penalty system in place. However, we had a traditional
arms-length vendor-client relationship, where feedback on service was
based heavily on crisis management and anecdotal failures with our most
vocal customers and sales people.”
That turned out to be an understatement,
with Swissport initially winning, then losing United, and customer issues
persisting to the present day; however, matters going forward are now
in the very capable hands of Jan Krems.
According
to Henrik Ambak, vice president Ground Services at Cargolux (an all-cargo
airline), “In principle we believe outsourced handling remains beneficial,
even for hubs, as internal units will typically not feel the competitive
forces required to keep them as fit as possible, be it in terms of customer
service or cost effectiveness. Over the past twenty years competition
has in many places brought a substantially lower unit cost, in particular
seen against the increase in labor costs experienced in the same period.
The challenges we have with outsourced handling can largely be resolved
if the airlines want to [fix it]. A key issue is structural, as many airlines
have an un-helpful segregation between procurement functions and Operations/Safety/Service
delivery. You typically get what you pay for, even in relative terms.”
Asked about the amount of overall management attention required, Henrik
said, “I personally spend around a third of my time on issues directly
related to handling agents.”
Especially at an all-cargo airline, the
decision is straightforward, as no one else needs to be consulted. For
combination carriers, sometimes the passenger side—good, bad, or,
indifferent—can dictate the choice of a handling company, with relatively
little clout to address problems as long as the passenger side is happy.
Another major carrier that operates both
freighters and also uses space on passenger aircraft recently commented
that while contracting at present with handling companies, they have been
mulling over the idea of insourcing handling at some strategic locations.
IATA plays a role in ground handling through
the IATA Ground Handling Council, and the IATA Safety Audit For Ground
Operations (ISAGO). According to IATA: “IGOM [IATA Ground Operations
Manual] has been developed in response to industry demands for enhanced
ground operational safety and damage reduction. IGOM is the core manual
for all ground operations and provides standard procedures for the frontline
personnel.”
Henrik Ambak told us “The AHM [airport
handling manual] will likely remain helpful, but of course the objective
is to get the IGOM to productivity so we can slim down our own carrier-unique
manuals and get ISAGO really going to finally bring the promised benefit.”
What do you think?
Ted Braun |